
Image courtesy of Terry Rossington
We’ve spoken to many mechanics and engineers during the course of our project. Our interviewees worked at a huge range of firms across the region and beyond. Examples include Atkins of Hinckley, Raywarp, Speedo, Wolsey, Corah, Meridian, Clutsom Penn and companies further afield such as the large American textile firm West Point-Pepperell Inc.
Most stayed for several years at one firm. The ex-employee from Atkins of Hinckley worked his way up from ‘tea boy’ to ‘Head Mechanic’ and described the firm as ‘the oldest hosiery company in the world’ established in 1723 (it was later bought out by Coats Viyella). Some started on formal apprenticeships, but most trained on the job with some college classes or training courses on specific machines. Those on apprenticeships praised this approach to training. As they progressed in their careers, many of them went on to train new apprentices or trainees on the ‘shop floor’. One described it as ‘heart-breaking’ when the company closed and all the employees he had trained were obliged to move on.
Our interviewees often described to us the importance of keeping the machines running, not only for the company, but for those who worked on them. These workers were usually paid piece rates (paid per item), and so a faulty machine would seriously affect their wages, and the wages of those ‘down the line’ who relied on a steady stream of items coming to them from other departments. For this reason, the machinists would often know a certain amount of maintenance techniques, but any more complex work would be done by the mechanics. A large company would often have a team of mechanics, and one recalled the practice of marking up tools so that their owners could be identified. He still has some of these tools from when he started in the trade.
Many mechanics and engineers were not just mending the machines, but also adapting them, developing new ways of doing things and often making their own replacement parts. Several of our interviewees described their involvement in developing new machines or adapting existing ones to perform new roles making processes more efficient. It was a task that did not always make them popular with the workforce, as they sometimes saw it as ‘putting them out of a job’.
The most mentioned factor in describing the atmosphere in the factories was the heat. An interviewee from our Belper event recalled: ‘… if a bearing had gone I was up against the wall by the motor…sweat dripping off me.’ Another described experiencing the ‘Pressing Room’s’ heat and steam, with the fans constantly working to cool it down, ‘the noise was horrendous’. Noise was another feature of life in the factory – one interviewee gave the sounds of the sewing machines this poetic description: ‘like a load of bees’. There were also a lot of references to the smell of oil and yarn.
Like all our interviewees, the mechanics reflected on the social side of work. Sports were very popular with the mechanics and engineers. One interviewee recalled playing cricket for Wolsey at their sports ground in Kimberley, but stressed it was a social event rather than competitive. Many of the larger companies had their own facilities. Speedo had a sports club and held an annual sports day. Meridian and Corah both had sports teams and club houses with ‘cheap beer, live music and dances at the weekends’, and the social club at Meridian was in existence ‘almost to the end’.
Many of our interviewees agreed that health and safety regulations have meant that this aspect of working with machinery had greatly changed over the years. The moving parts now have guards, and hands are protected from cutting equipment by ‘chain mail’ gloves. In our interviews with all workers, one of the most described injuries was the ‘needle through the finger’, which, we were told, is now prevented by the installation of needle-guards. One interviewee goes as far as to say that the changes in safety around the machines were greater than the alterations to the machines themselves.
One of the obvious changes over the years is computerisation. One of our interviewees recalled some machines that were considered ‘high-tech’ at the time, but would seem very out-dated today. The introduction of computers meant that machines could become more complex, handling more advanced patterns (a key advance for lace machines). Most of our interviewees embraced the new technology as it emerged, and acknowledge that there have been huge changes in this area over time, but as one of them points out ‘… they still do the same job’ and ‘they’ve not got a machine yet that doesn’t break’.
As moves toward off-shore production picked up speed in the 1980s, many textile workers joined the National Buy British campaign’s march on Nottingham market Square, but despite the protests, many firms moved their production or sold their machines abroad. Their working lives intertwined with the technology, the engineers often uprooted and went with them, to teach their skills to the new mechanics/operators. This was the case for a few of our interviewees, but we also heard opposing opinions, in a landscape of turmoil in the industry, feelings ran high and there was a view from some that going abroad to pass on skills would ‘put you out of a job’. Others saw it as evolving with the industry or as a means of continuing in your role for as long as possible. Some production was sometimes kept in this country, involving a requirement to travel abroad to the factories to resolve problems, but not a permanent move. Several of our interviewees describe the disappointment of losing the industry, and often compare the decline of textiles to the mining industry. There is a strong sense of grief as they tell us how some of the machines they cared for were smashed up towards the end of the factory’s life.
Perhaps the mechanics and engineers were able to transfer their skills more easily to other industries than some of the other textile workers, but our interviewees all reflected on their time in the textile trade with fondness. One of them stated that he had enjoyed his career, would do the same again, and still sees people he used to work with. He attributed this friendship to the nature of the work: ‘you had to help each other because some of the problems were in-depth technical problems on the machines’. Another, having left the industry to start his own business in a different trade, told us that he still goes back to help out his old firm when they need it because ‘it’s in your blood’.
article by Tonya Outtram
One of the engineers we interviewed at Loughborough describes helping each other out with technical problems. He mentions the companies Rimoldi and Union Special.
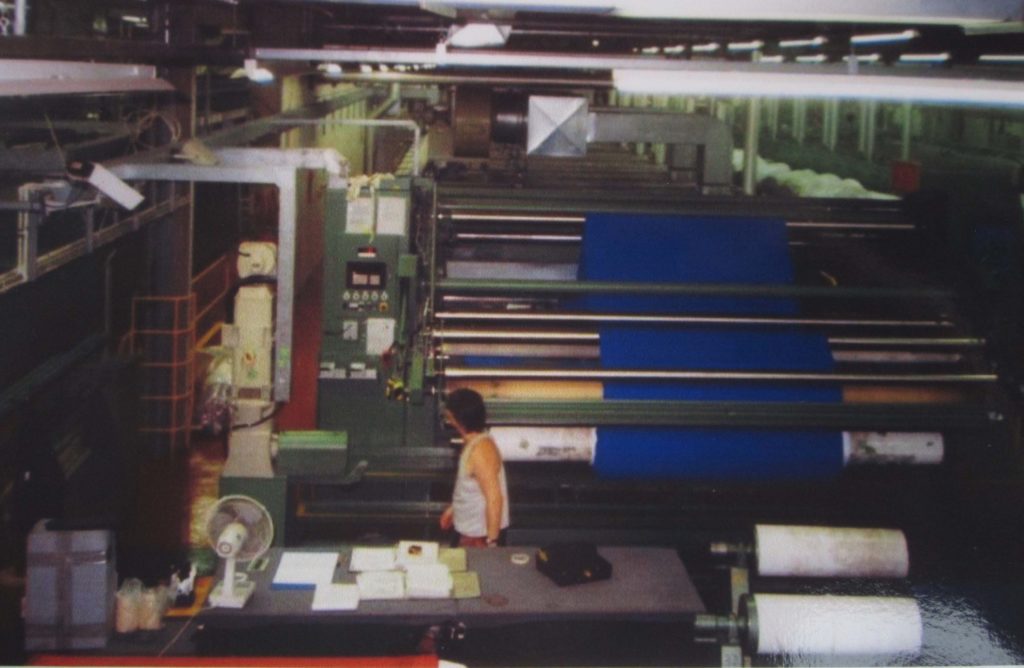
Penn Nyla, Trentham factory, 1999. Image courtesy of Anne Higton